Upal Sengupta, Staff Applications Engineer
Texas Instruments
Some years ago, we started saying the phrase “plug and play” to describe anything that was easy to use. Compared to the good old days, many of today’s complex devices are substantially easier to set up, configure and start using than previously. Today, customers expect a product to be ready to go “out of the box.” More than ever these expectations are being met, at least to a reasonable degree. When was the last time you had to read a user’s manual before you started playing with a new gadget? However, this outward simplicity is a bit deceptive. As engineers, we must take more care to make our products easy to use from the outside, despite all the complexity they may have on the inside.
Following this trend, IC component suppliers have tried to make their parts easier to use for system designers. Compared to the (not-so-distant) past, most IC data sheets have detailed design equations, external component selection guidelines, and even suggested PCB layout diagrams to facilitate incorporating a given IC into a system-level design. Almost all catalog IC devices have evaluation kits available to help system designers learn the details they need before committing to their own PCB construction.
Unfortunately, sometimes system design engineers fall into the trap of assuming that the IC components they use in their equipment designs are also “plug and play.” It is easy to assume that if you just “connect the dots” in the same way that is shown in the application diagram from the IC’s data sheet, you won’t have to do any additional analysis or validation of your design. But while the guidelines and suggestions provided in modern IC data sheets might simplify system design, they don’t entirely eliminate the work that needs to be done by the product design engineer.
Designing the power system for battery-operated equipment consists of two major sections. First, we have to choose the right type of battery technology and pack design. Second, we have to develop the electronic circuitry to charge that battery pack and convert the battery’s unregulated “raw” voltage into the regulated output rails needed to operate the actual system electronics. Last month, we talked about the importance of choosing the right type of battery technology as the first step. Once we do this, then the “real work” begins.
A very common oversight is the lack of thermal analysis. In particular, for very low-power battery-operated equipment, it’s easy to think that the power levels are not high enough to worry about thermal management. However, remember that the power density of these handheld systems can actually be quite high.
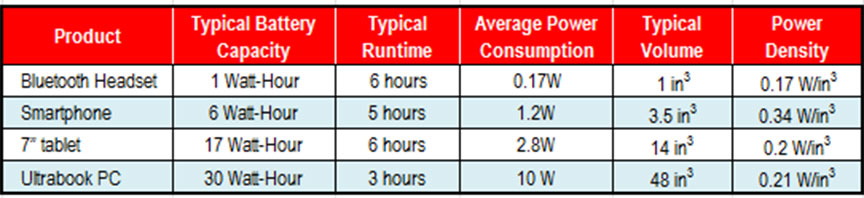
Table 1 shows us that even devices with low absolute power consumption need to be carefully designed, keeping thermal management in mind. Remember, we are cramming that low power consumption into a very tiny space. For higher power devices such as ultrabooks, notebooks and computers, heat dissipation is quite noticeable. The device actually feels warm to the touch. For lower power devices, with only milliwatts of internal dissipation, the end-user may not feel the unit case getting hot. However, if the dissipation in the low-power circuitry is localized to a small “hot spot” inside the unit, there may be concerns associated with device reliability or usability. This is especially true if the semiconductor components are being operated closer to (or above) the recommended thermal limits.
In the past, with large semiconductor packages and the option for external “bolt-on” heatsinks when needed, we may not have thought too much about circuits that dissipated only milliwatts. But for high-density portable products, in particular those without internal cooling fans, the only practical heatsinking available is to use a copper layer in the PCB itself.
The copper plane typically is located on the opposite side of the PCB from the components. Hence, thermal vias are needed to connect the thermal pads on the surface mount ICs to the heatsinking plane. Figure 1 illustrates how thermal vias can be used to route heat away from an IC. Most of the heat is spread out through thermal conduction, so we want to minimize thermal resistance in the path from the IC’s power pad to the copper layer on the other side of the PCB. This is done by paralleling multiple thermal vias connected to the IC that can channel heat away from the package.
- Figure 1. Thermal conduction paths for surface mount PCB.
Doing a full, accurate thermal simulation of your PCB design can be a complex process requiring sophisticated thermal analysis software, often beyond the scope (and budget) of many projects. However, following the equations and layout guidelines provided in an IC data sheet usually gives the system designer a good chance of “first-pass success” with his/her power supply design. Furthermore, it is a straightforward process to calculate the effective thermal resistance of the thermal vias, copper traces, and copper plane areas available on the system PCB. By following the techniques described in detail in the following references, a system designer can get a much higher level of confidence in proceeding with a board layout for power conversion circuits.
References
- “Constructing Your Power Supply: Layout Considerations,” Robert Kollman, Texas Instruments, 2005:
- “Thermal Considerations for Surface Mount Layouts,” Charles Mauney, Texas Instruments, 2006:
- “AN-2020: Thermal Design by Insight, Not Hindsight,” Marc Davis-Marsh, Application Report (SNVA419B), Texas Instruments, June 2011
For more information, visit www.ti.com/battery-ca.
Upal Sengupta is a staff applications engineer with the TI Battery Management Solutions group. Since joining TI in 2003, Upal has worked as an applications engineer and technical marketing manager in support of TI’s portable power and battery management technology. Prior to TI, he worked as a system design engineer for OEMs developing mobile phones, portable computers, and consumer products. Upal received a BSEE from the University of Illinois, and an MSEE from Michigan State University. Upal can be reached at ti_upalsengupta@list.ti.com.