Contributed Commentary by Marvin Ho, VP Product Engineering and Quality at U.S. Battery Manufacturing
October 7, 2024 | A few years ago, there was a rush within the battery industry to be the first to have a deep-cycle lithium-ion battery for a variety of industrial and energy storage uses. The result was an abundance of batteries that quickly flooded the market. On the surface, many seem similar, but differences in lithium cell types and mechanical configurations matter, especially when reliability, capacity, and service life matter.
Teardown testing of several lithium-ion batteries showcases the wide variety of designs and hardware quality. For anyone in the market for a deep-cycle lithium chemistry battery, it’s important to know that battery manufacturers can utilize a variety of cell designs and construction. Understanding what components are used in these batteries can help you make an informed decision, rather than basing it on price alone.
Cell Comparisons
Deep-Cycle lithium batteries are available in 12, 24, and 48-volt models, depending on the application. They also range in advertised capacity from 60–105 amp hours (Ah). While it’s easy to select a battery based on voltage and how many Ah are required, there are differences in the types of cells used in the battery.
A Cylindrical Cell is a common lithium battery cell, similar in size and shape to an AA battery. A deep-cycle lithium battery made of cylindrical cells typically requires welding hundreds of these individual cells in series/parallel to achieve the required voltage and capacity. A look inside a 12-volt deep-cycle battery with these cells showcases the number of cells needed, and how they are connected.
Prismatic LFP Cells are another type of lithium battery cell, but these are the size of a paperback book or stack of index cards. Because these cells are larger, they contain more energy per cell than cylindrical cells. Therefore, fewer Prismatic cells are needed to achieve the same amount of capacity, voltage, and advertised Ah rating. Looking at a disassembled 12-volt deep-cycle battery with Prismatic Cells, you can see there are fewer individual cells and in this case, there are a total of 16 cells connected in series.
Connectivity
The method in which any type of lithium battery cells are internally connected also makes a difference in the battery’s reliability and performance. Manufacturers using Prismatic Cells typically connect them using laser welds for precision and consistency. This provides high shock and vibration resistance, which is important in some applications such as golf cars, aerial platforms, floor-cleaning machines, and RVs.
By comparison, lithium batteries using cylindrical cells often have spot-welded connections that are small and have a limited contact area. This can make them susceptible to detachment from consistent vibrations. The thickness of the material used to weld cells together also matters, as some manufacturers use thin metal sheets to connect the cylindrical cells. This method makes them susceptible to overheating, which can shorten battery life. Thicker connections, commonly used on Prismatic Cells are great for high amp loads, often seen with batteries used in heavy-duty industrial applications such as cranes, forklifts, or electric vehicles while they are climbing hills or hauling heavy loads.
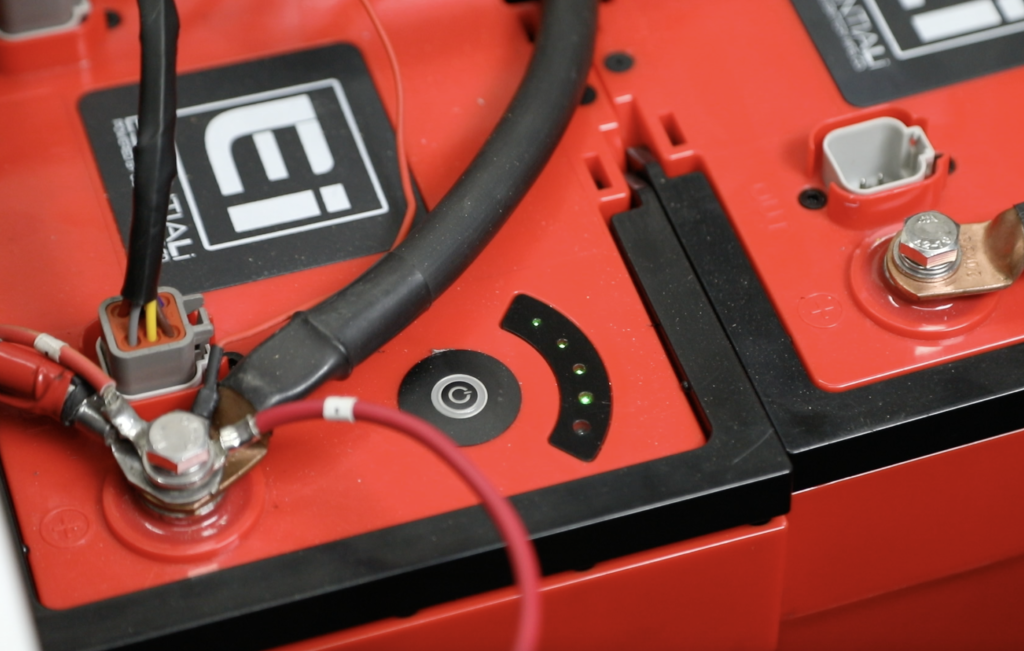
The Battery Management System (BMS) used in lithium batteries can also range from a sophisticated unit for special applications, to basic off-the-shelf systems designed for multiple uses. On lithium-ion batteries, cell voltage must be consistently monitored accurately to preserve the safety and life of the battery. Each cell is not identical, and during operation, the cells naturally drift apart in voltage, requiring a correction to keep them properly balanced. This correction is accomplished by discharging higher cells at the end of the charge.
So a quality BMS should also have high-quality voltage sensing leads with robust connections and wiring that are bolted and/or welded to the cells. Settling for lower cost hardware, as seen in some teardown comparisons, could give false cell voltage readings and lead to premature failures.
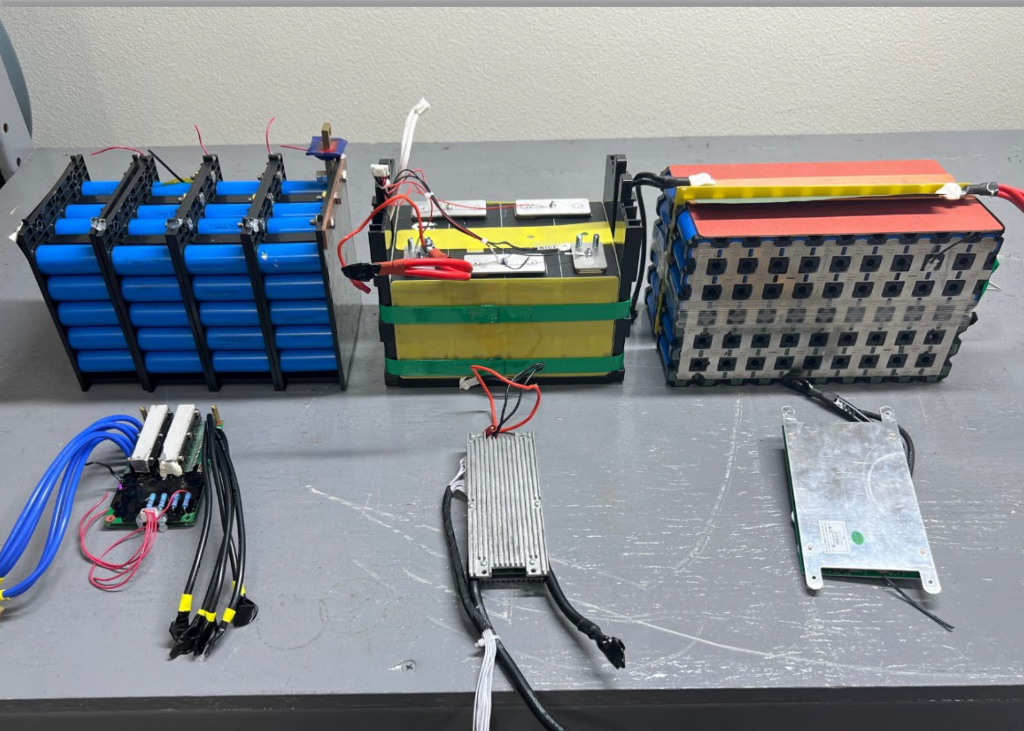
Controlling heat during charging and discharging is also a critical aspect of the BMS. During both of these processes, heat from battery cells and any connected electronics, is an expected aspect of normal operation. Various battery manufacturers use heat sinks to improve the BMS’s ability to manage heat and hardware stability.
Teardown comparisons, show the various types of heat sinks, if any, used on BMS units. We’ve seen that some battery manufacturers use minimal or no heat sinks, while others use thick aluminum sinks with fins to dissipate heat quickly. The BMS should also have sensors to monitor the temperature of cells and electronics. Obviously multiple sensors are better than one, making it another indication of quality when comparing batteries. The average consumer can’t see these types of construction so it’s important to ask your battery dealer what heat sinks are used on the BMS when comparing batteries.
One key feature to look for in a high-quality deep-cycle lithium-ion battery is the ability to determine battery status. A sophisticated BMS will have an LED light function on top of the battery case, indicating its condition or state of charge. It can also alert to any problems with the battery or connections to it. Some also include an on/off button on top of the battery, allowing you to save power when the battery is not in use or for long periods of storage. Other types of BMS systems feature wireless connection to a mobile phone app to provide battery information to the owner/operator.
If you want to take advantage of lithium deep-cycle battery technology, it’s important to ask your battery dealer about general battery construction. If they are unfamiliar or can’t get you that information, research the battery info from the manufacturer’s websites. Then, ask your dealer about the differences between battery brands and look for those that provide the highest quality and reliability for your money.
Marvin Ho is the Vice President of Product Engineering and Quality at U.S. Battery Manufacturing. With a Ph.D. from The University of South Carolina in Chemical Engineering, Ho manages Research and Development of U.S. Battery Manufacturing’s Essential Li line of deep-cycle lithium-ion batteries. He can be reached at mho@usbattery.com.