May 19, 2018 | News Brief | It’s great in the lab, but will it actually work? That’s the million-dollar question perpetually leveled at engineering researchers. For a family of layered nanomaterials, developed and studied at Drexel University — and heralded as the future of energy storage — that answer is now, yes.
For some time, researchers have been working on using two-dimensional materials, atomically thin nanomaterials, as components for faster-charging, longer-lasting batteries and supercapacitors. But the problem with the existing techniques for doing so are that when the thickness of the material layer is increased to about 100 microns, roughly the width of a human hair, which is the industry standard for energy storage devices — the materials lose their functionality.
Recently published research from Drexel and the University of Pennsylvania, shows a new technique for manipulating two-dimensional materials that allows them to be shaped into films of a practically usable thickness, while maintaining the properties that make them exceptional candidates for use in supercapacitor electrodes.
The study focuses on using soft materials, similar to those in the liquid crystal displays of phones and televisions, as a guide for self-assembly of MXene sheets. MXenes, are a class of nanomaterials discovered at Drexel in 2011, that are particularly well-suited for energy storage.
“Our method relies on a marriage between soft material assembly and functional 2-D nanomaterials,” said Yury Gogotsi, PhD, Distinguished University and Bach professor in Drexel’s College of Engineering, who was a co-author of the research. “The resulting electrode films show rapid ion transport, outstanding rate handling, and charge storage equal to or exceeding commercial carbon electrodes.”
An Open Channel
According to co-author Yu Xia, PhD, a postdoctoral fellow in Penn’s School of Engineering and Applied Science, the challenge of maintaining the energy density (how much energy the devices can store) and power density (how fast the device can charge) of a charge storing material lies in maintaining clear channels for ion movement as the materials are scaled up to larger sizes.
“The ion diffusion problem in energy storage devices,” Xia said, “including batteries and supercapacitors, has been long recognized as one of the major issues impeding the industrial development of new batteries and supercapacitors with higher energy and power density. Conventionally, 2-D materials intend to stack on top of each other like sheets of paper in a book, resulting in a prolonged ion diffusion length, which suppresses their performance when the thickness of the electrode approaches industrial standards.”
The team’s method avoids this stacking problem, which inhibits ion diffusion, by propping the MXene flakes in the electrodes vertically. At the microscopic level, it might look something like standing up toothpicks in silly putty. In addition to getting them to align vertically, their orientation can also be adjusted by moving the soft material base.
The team’s melding of soft matter assembly with hard materials yielded promising results for MXene’s future as an energy storage material.
“MXene electrodes prepared by this method show normalized capacitance which is almost independent of thickness up to at least 200 microns, which is not the case for conventionally assembled electrodes, where the MXene flakes would be aligned parallel to the electrode surface,” according to Tyler Mathis, a doctoral student in Drexel’s Department of Materials Science and Engineering and co-author of the research, who performed all electrochemical testing of the materials.
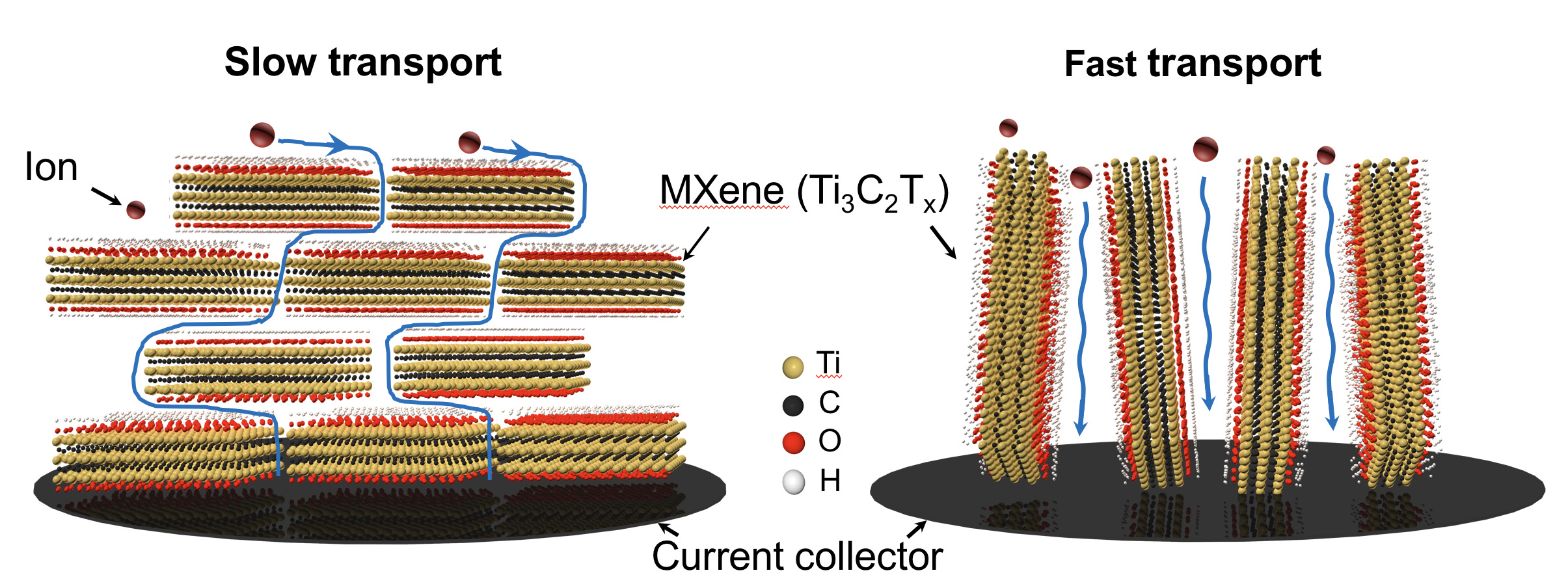
Stand and Deliver
While “soft matter self-assembly”, the process by which molecules inside a material align themselves in an orientation that researchers can manipulate, has been around since the 1970s, and is now the driving force behind television, phone and laptop displays, combining it with hard materials is a significant breakthrough.
Although a couple of research groups have been able to engineer vertical alignment of materials using a top-down process, these routes are difficult to scale up for industrial applications.
“Our process is through self-assembly,” said Shu Yang, PhD, a professor in the departments of Materials Science and Engineering, and Chemical and Biomolecular Engineering in Penn’s School of Engineering and Applied Science and a co-author of the research. “So it’s much cheaper and can be scalable over a large area. In the end, it’s the concept of using soft materials with interesting alignment and ordering through assembly to align hard materials with interesting nanostructures and functionality that is the biggest breakthrough.”
To get the 2-D material to undergo this process, the researchers used a surfactant, which can squeeze between the MXene layers to help them form a liquid crystal phase. The researchers then applied a mechanical shearing method to it, which forced the molecules to align the MXene films vertically. The vertical channels allow ions to move, or diffuse, which is the key to MXene’s properties, even as the material is scaled up in thickness.
“There’s a lot of fundamental knowledge in liquid crystals,” Yang said. “People think it’s an old technology, but we just keep rediscovering that this knowledge is actually very useful and applicable to new functional materials.”
Next in Line
Although the researchers acknowledge that there are other challenges to overcome before the method can be used in real world devices, they believe their findings provide an exciting leap forward in the field. The long-term goals are to apply the method to supercapacitor and battery electrodes for powering mobile electronic devices, electric cars, and use in renewable energy harvesting technologies.
“It’s a perfect marriage between soft matter self-assembly and nanomaterials,” Xia said. “We’re making a new world of these 2-D materials that can be used towards real industry applications, matching up with the industry standard and trying to make a real device out of it. After more than a decade of work in 2-D materials, we have found a way past one of the biggest barriers to application and are actually creating a system that is one of the most plausible ways to push these materials into industry.”