E.J. Spek, Chief Engineer, TÜV SÜD Canada, Inc.
Customers of car companies have come to expect vehicles that are considered safe, according to a catalog of standards. Hybrid, plug-in hybrid and battery electric vehicles are and will be subject to the same expectations.
The standards that have been developed for more than 100 years for combustion-engine vehicles have been effective in ensuring that the vehicles are indeed considered safe. These same standards need to be augmented to account for the electrification component that comes with high voltage and significant amounts of stored electrical energy. The risks that have been introduced in these electrified vehicles need to be considered in the design and development phase of the automotive product development process. The task of writing and then proving out these standards is a slow and laborious process. It has taken more than 10 years of work by a number of regulatory and certification bodies to produce a considerable number of relevant standards documents. Notwithstanding the pioneering yet thorough effort, there are a number of issues that need to be addressed to make the final standards robust, consistent and universal. Central to the effectiveness of the standards are the test methods used to verify that the product satisfies the requirements as defined by the standards. Some of the first organizations to implement the test methods are third party test agencies. These organizations can be very helpful in identifying test method shortcomings and opportunities for improvement. TÜV SÜD is one of those organizations.
TÜV SÜD is a third-party ISO 17025-certified global testing company that performs battery testing for several organizations in the mobile, stationary and consumer products fields. Abuse tests are conducted to establish the reaction of cells, modules or batteries to conditions exceeding those expected to be encountered in normal vehicular use. This information can then be used to make decisions in the design or design verification process. This is especially important for lithium-ion products that do not yet have an established track record of safe operation over many years of service and abuse conditions.
One of the common abuse tests conducted at TÜV SÜD is the nail penetration test as described in SAE J2464 section 4.3.3. The short history of lithium-ion battery development, especially in large ampere-hour and pouch cells, is one reason that the current state of cell nail penetration test specifications is substantially open to interpretation in test methodology. TÜV SÜD, in actively supporting the electric vehicle industry, has pursued a path of continuous test methodology improvement for the cell penetration test over the last two years. After having abuse-tested hundreds of large format lithium-ion cells, TÜV SÜD has a robust and repeatable process to support rapid cell development and verification testing. The hurdles that TÜV SÜD has encountered in making this test effective are described qualitatively below. It is hoped that others engaged in a similar improvement process can benefit from the knowledge gained.
Recommended Practice
SAE (Society of Automotive Engineers) has a recommended practice in SAE J2464 that describes a nail penetration test in section 4.3.3. The description includes the parameters as listed in Table 1 for cells. Other values are used for modules and packs.
Test Methodology History
TÜV SÜD has primarily tested both hard case and soft prismatic (pouch) cells for nail penetration. The first TÜV SÜD test device for the penetration test was an air-driven cylinder set at a nail velocity of 100 cm/sec. This high value was used to ensure that the minimum nail velocity through the actual penetration of cells as thick as 12 mm would be above the minimum specified 8 cm/sec. Note that in a vehicle, the bare cells are protected from flying objects by the pack structure, this explains the relatively low velocity value compared to road speed.
Since the force capable of being produced by the air cylinder was substantial at 1.5 kN, there was no concern for a slowing down of the nail through the cell thickness to less than 8 cm/sec. A substantial number of cells were tested in this manner but results at EUCAR 5 and 6 could not be correlated to cell suppliers’ similar penetration test data.
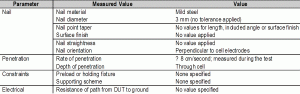
In a concerted effort to resolve the discrepancies, many of the characteristics listed in Table 1 as ‘no value’ were given values based on successful tests given an arbitrary assignment of EUCAR Hazard Severity levels of less than five as ‘acceptable’.
The following were given initial values: nail surface finish, point included angle and surface finish, material selection within steel, nail straightness and perpendicularity, cell preload and cell restraint method. With these refinements, more cells were tested from selected anode and cathode chemistries as well as capacities. Concurrently, the rate of penetration in open air was reduced from the 100 cm/sec to the minimum 8 cm/sec to be aligned with the cell supplier’s nail velocity. With the implementation of these test method changes at both the TÜV SÜD and a selected cell supplier’s lab, the cell supplier’s data became more aligned with TÜV SÜD.
In planning ahead for penetration testing on thicker and multiple-stacked lithium-ion cells as would be found in modules, the air system for driving the nail was replaced with a hydraulically driven system capable of delivering 45 kN with precise control of speed, acceleration and depth of penetration. This comprehensive system was then used on a large number of cells, but discrepancies between this system and the air system emerged under otherwise apparently identical parameters. Efforts to determine the key differences in the methodologies were then carried out focusing on nail geometry, ambient vibrations, test temperatures at the cell locale including supporting platen and chamber, electrical isolation and ground path of the DUT (device under test) to platen, DUT mounting features, path of the nail (misalignment and potential of dragging through the DUT) and test operator training. As a result of this work, all identifiable differences were either eliminated or accepted as being of minor influence. In spite of all these test homologation efforts, the hydraulic system test reactions were markedly different than the air drive system.
A subsequent analysis was carried out to verify the velocities of the air system and the hydraulic system using four independent methods. These included the integral LVDT output of the hydraulic cylinder, a linear potentiometer on air and hydraulic systems, an independent LVDT, and a light sensitive speed trap. Good measurement concurrence on velocity was achieved between all of these. The linear string potentiometer was also used to assess any slowing- down effect of the resistance of the cell on the air system. This revealed that at the initial 8 cm/sec setting, the speed reduced to 5 cm/sec partway through the cell thickness. In order to elevate this value to the >8 cm/sec specification, the initial speed of the air cylinder would have needed to be raised in an iterative process on real cells, which were not available in sufficient quantity. This also validates the change to the more capable hydraulic system with its negligible sensitivity of velocity to cell thickness compared to the through the air nail velocity. The conclusion from the work to date is that the hydraulic system is the most robust and consistent for nail penetration tests on pouch cells.
This finding along with other TÜV SÜD tests carried out to date indicate that any other penetration testing performed at less than 8 cm/sec may be suspect by presenting a false mild reaction. Moving forward however, the need to establish test outcome sensitivity to nail speed seems to be critical for cell developers.
Unidentified Influences on EUCAR Reaction Level
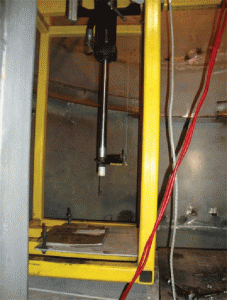
Beyond the analysis, it was apparent that one or more parameters were influencing the reactions of the cells to the nail penetration. In another side-by-side comparison, where the air-driven system was used to test first a cell with fixture mounted on an abuse chamber table (Setup 1) and then, second, the same kind of cell in the same fixture but mounted on the open bottom hydraulic fixture (Setup 2), the table test produced a Hazard Severity Level (HSL) 1 reaction, while the other produced an HSL 5-6 reaction. These values are also referred to as EUCAR as well as HSL.
With such a markedly different result with fundamentally the same setup, another examination for possible differences was undertaken. Using test video files as a tool and examining the test setup again, it became apparent that the only visible difference occurred in the test setup wherein the underside of the cell was completely open to the air in Setup 2, while the underside of the cell in Setup 1 was substantially closed to air.
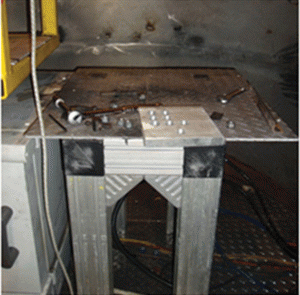
The videos of similar tests showed that as the nail penetrated the underside of the cell, a flame escaped downwards into the air gap (Setup 2). This was followed by a second flame escaping upwards from the top side of the cell. From this observation, a hypothesis was developed that suggested that the small air gap had a quenching effect on the downward flame as compared to Setup 2 where there was no quenching effect. The quenching effect may also be related to the possible lack of stoichiometric (fuel-rich) mixture of oxygen and electrolyte vapor in the small air gap. While this hypothesis has not been proven, it highlights a possible direction for further work. It is encouraging to note that most professionally designed battery packs will have very little open volume inside and thus may react more favorably. Note that similar work conducted by TÜV SÜD Battery Testing in Germany has raised the hypothesis that under some conditions, the cell anode may release graphite powder and exacerbate the EUCAR level.
Need for More Exact Specification
The efforts described in this white paper demonstrate the importance of refining the standard/recommended practice to a specification. If each and every cell and battery manufacturer and testing provider develops unique abuse testing methodology, the implied cost and extended development timelines will be onerous. The question of why cells react as they do to this kind of abuse test remains unanswered, and TÜV SÜD is pleased to be working with other organizations to apply its skills in battery engineering and primary postmortem analysis to help observe, analyze and guide further investigations.
For more information, please visit http://tuvcanada.ca.
This article was printed in the March/April issue of Battery Power magazine.