Commentary Contributed by O. El Baradai, J. Schleuniger*, S. Fricke, C. Bosshard, CSEM SA, Switzerland
October 24, 2017 | Continuous progress in electronic devices, in particular portable electronic gadgets, is creating new opportunities and products to revolutionize our daily life. However, these ubiquitous portable devices with different functions require highly efficient power sources to sustain their use. Batteries are essential for powering such portable electronic devices. A battery is a closed system in which energy is stored in chemical form, and it is converted to electrical energy by connecting the battery to an external load to complete the circuit, causing electric current to flow between the anode and cathode. Electronics have traditionally been designed around commercial batteries:prismatic, cylindrical, and coin cells, which are bulky, rigid, and non-flexible, making them unsuitable for powering flexible electronics. In particular lithium-ion batteries (LIBs), as the main power source, dominate the portable device market due to their high energy density, high output voltage, long life, and environmentally friendly operation. In order to further facilitate their portability, the trend in LIBs development is to light, thin, flexible, and small units, while currently the most commonly used ones are still too heavy, thick, rigid, and bulky to match practical requirements. Innovation in battery technology and the strong consumer market demand for portable, ultrathin and flexible devices, such as roll-up displays, touch screens, active radio-frequency identification tags (RFID), smart electronics, wearable sensors, and implantable medical devices, are driving the rapid development of flexible electronics. Some concept and prototype of flexible electronics have been demonstrated
Samsung has demonstrated a new bendable organic light emitting diode display technology and a prototype flexible device running Windows Phone, which allow users to bend the screen back and forth with ease [1]. These portable flexible electronic products are considered a revolutionary invention after notebook computers and mobile phones, that will be widely used and influence future life styles.
For this reason, flexible energy storage and power sources, such as flexible LIBs with various sizes, shapes, and mechanical properties are urgently required for the development of bendable, implantable, and wearable electronic products. The key challenge to realize flexible batteries is to design and fabricate reliable materials with high capacity, high rate capability, cycling stability, good conductivity, and robust flexibility, coupled with high performance electrolytes and separators in a rational assembly. A paramount requirement for a flexible LIB is that the power and energy supply as well as cyclic stability are not compromised under frequent mechanical strains, such as under bending, twisting, or other deformation modes for long term use [2].
Another paramount requirement is the reduction of the environmental impact in the production and disposal of LIBs. Because of its low cost and large availability, cellulose, and its derivatives have been successfully used in LIBs for the fabrication of electrodes, separators, reinforced gel, or dried polymer electrolytes [3]. The use of cellulose derivatives allows a “greener” processing since the ink formulation does not require the use of volatile and toxic organic solvent. Eco-friendly inks have been formulated using water as solvent and cellulose derivatives as dispersing agent. Concerning the manufacturing process, printing processes have been selected as a very economic production method and they play a more and more important role in LIBs manufacturing strategies. Contrary to the coating method, printing techniques allow the elaboration of patterns on different substrates with minimal extra cost production. The properties of printed films strongly depend on the viscosity and the composition of the ink. An appropriate formulation protocol can lead to gain in performances in terms of charge and discharge capacity whereas mixing influences key parameters as cyclability and rate capability. In terms of packaging solutions, flexible assembling designs have been proposed in the last years to overcome limitations due to mechanical stresses and shape requirements in LIBs manufacturing processes . Eco-friendly electrodes using inks having water as solvent and cellulose derivatives as dispersing agent has been reported for the positive and negative electrode with promising results [4], [5].
Here we developed a LIB based on a new assembling strategy where positive and negative electrodes are printed on the front / reverse side of the separator. New functional inks were formulated by replacing conventional fluorine based binder (PVdF) and toxic solvent (NMP), with bio-sourced cellulose derivatives as carboxymethyl cellulose (CMC) having the role of dispersing, micro fibrillated cellulose (MFC) as binder and aqueous solvent. Screen printing was selected as electrode manufacturing process because of its versatility and ability to deposit thick films thus insuring a high content of active material. Furthermore, a new assembling strategy, based on the printing of bio-sourced current collector ink in the inner side of the pouch was proposed in order to have a one-step printing and assembling process.
Results
Firstly, a rheological study has been performed to investigate the influence of carboxymethyl (CMC) and microfibrillated (MFC) cellulose components used as a disperser and binder respectively. In order to increase the performance, the content of graphite and (GP) and Lithium iron phosphate (LFP) active materials has to be maximized. We performed a preliminary investigation to determine the optimal solid material content (Ms) and the appropriate dispersion protocol, a range of formulations have been investigated in line with the rheological properties required by the screen printing process:
The appropriate Ms percentage, in line with the rheological properties of the screen printing process has been identified. Secondly, the impact of the conductive particles content on the electrical properties has been investigated; the content of the disperser and the binder was not changed. In order to fit the rheological requirement for the screen printing process, the content of the conductive particles in the formulated inks has been tailored to reach a value ensuring simultaneously optimal printability and electrical conductivity.
The same approach has been used also for the formulation of the current collector ink. In this case, because of its electrical conductivity, graphite component (GP) was maximized to ensure a good conductivity of inks. A study has been realized to find the best additive materials that can be used as conductive agent to enhance the electrical properties For this purpose aluminum (Al) and copper (Cu) particles, generally used as current collectors, seems to be the best candidate for the formulation of water based inks and printing of current collector layers. However the inherent tendency of Al and Cu particles to oxidize, especially in water medium obliges to the use of expensive formulation process. For this reason we focused our attention on carbon based particles as graphite (GP), carbon black (CB), and carbon nanotube (CNT) that are relatively easily dispersible in water medium and can act as current collectors for both electrodes.
The graph in Figure 1 shows the measured electrical conductivities for the CB and CNT based inks, The CB has a greater impact on the electrical properties, this phenomenon might be ascribed to the fractal structure of CB that promote the contact between graphite particles and ensure a uniform current density.
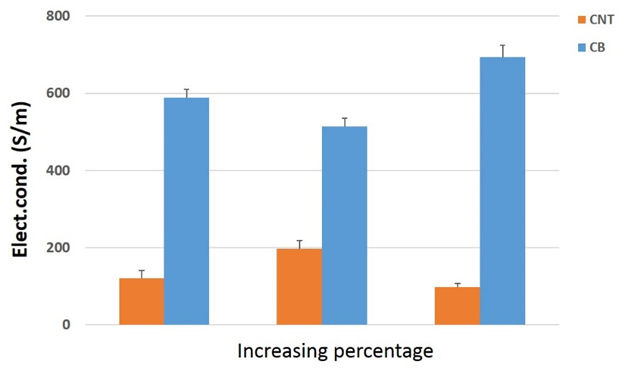
Due to the results obtained it was possible to determine the optimal content of CB ensuring a high electrical conductivity and it will be used as potential current collector ink.
To ensure the formulation of water based inks having the rheological properties demanded by the screen printing process used in this work, an analysis has been performed to investigate the impact of carbon black (CB) and carbon nanotube (CNT) particles as a rheological enhancer. A steady state study has been performed to analyze the response of the ink to shear rate variation. The ink viscosity has been characterized by measuring rheological properties in a shear rate ramp ranging from 1 to 1000 s-1 (orange curve) and 1000 to 1 s-1 (blue curve). 1000 s-1 has been selected as maximum shear rate, because it is the highest shear value typically reached in a screen printing process. The absence of hysteresis loop was a proof of the optimal rheological properties of the inks.
Secondly the inks, printed onto the cellulosic based separator were characterized electrochemically for positive and negative electrode performances in “half cell” configuration. The negative electrode exhibited the characteristic oxidation and reduction peaks of graphite based electrodes. The first voltammetry cycle showed the classical profile of a first activation of the electrode with the formation of a solid electrolyte interphase (SEI) layer on graphite based electrodes. Repetitive charge and discharge cycles have been performed and mismatch between curves, due to side reactions during cycling has not been observed. Concerning the positive electrode, the discharge profile revealed a specific capacity value of 150 mAh/g in line with the value stated by the supplier for the active material used in this project.
The mechanical properties of the electrodes have been tested by stress–strain and bendability test. As known the formation of cracking due to repetitive bending impacts the electrical conductivity of the electrodes. For this reason we analyzed the evolution of the electrical conductivity as function of the number of bending. Owing to the elastic properties of the graphite particles, the electrical conductivity was not affected by the number of a bending cycles at the bending radius of 1.5 cm as shown in Figure 2.a. However the electrical conductivity of the positive electrode seemed to be affected by the bending of the cell as displayed in Figure 2.b. In fact a reduction of 14 percent of the electrical conductivity has been measured. Contrary to graphite, the lithium iron phosphate (LFP) particles are more fragile and the electrical conductivity might be reduced in case of fractures inside the electrode.
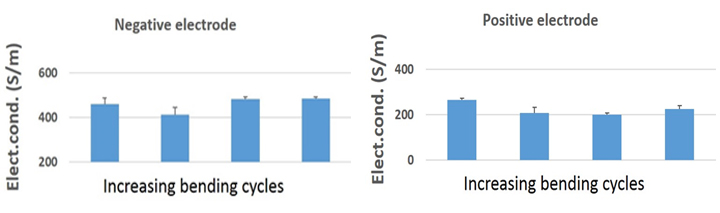
As described previously one of the objective of this work was the replacement of the current collectors with conductive inks. The mechanical properties have been tested by printing the current collectors onto the packaging of the cell, in order to determine the response to repetitive bending. The results revealed, similar to the graphite based conductive inks, appreciable elastic properties without fading of the ultimate tensile strength after a high number of cycles.
For the assembly of full cells, the positive and negative electrodes have been printed onto the separator in order to use it not only as physical barrier avoiding potential short circuit between the electrodes, but also as a substrate to print the components of the cell. The thickness of the separator has been tuned in order to avoid any potential short circuits in the system.
A full printed cell has been tested no side reactions has been observed during the charging of the cell. Even after a charge and discharge cycle of the cell, the open circuit voltage (OCV) was 3.15 V, in line with the expected value for lithium ion technology. The galvanostatic behavior of the full lithium ion cell reached at the first charge of the cell is 110 mAh/g. The electrochemical properties have been also investigated by means of impedance spectroscopy and galvanostatic measurements of the full lithium ion cell. An internal resistance of 300 Ohm was measured in line with the results generally reported for thin lithium ion batteries. However, further improvement has to be done in order to increase the reliability of the prototype.
Conclusion
The results achieved in the project demonstrated the feasibility of printed lithium ion batteries by an up scalable process such as screen printing and the use of bio-sourced materials. The electrochemical, mechanical and electrical results are in line with the conventional batteries produced by other technologies such as blade coating and represent a viable route for the elaboration of thin lithium ion batteries. Further work is currently in progress to improve the reliability of the prototype in order to conceive batteries in line with the market expectations.
References
[1] G. Zhou, F. Li, and H.-M. Cheng, “Progress in flexible lithium batteries and future prospects,” Energy Env. Sci, vol. 7, no. 4, pp. 1307–1338, 2014.
[2] H. Gwon, J. Hong, H. Kim, D.-H. Seo, S. Jeon, and K. Kang, “Recent progress on flexible lithium rechargeable batteries,” Energy Env. Sci, vol. 7, no. 2, pp. 538–551, 2014.
[3] A. M. Gaikwad, H. N. Chu, R. Qeraj, A. M. Zamarayeva, and D. A. Steingart, “Reinforced Electrode Architecture for a Flexible Battery with Paperlike Characteristics,” Energy Technol., vol. 1, no. 2–3, pp. 177–185, Mar. 2013.
[4] O. El Baradai, D. Beneventi, F. Alloin, Y. Bultel, M. Party, and D. Chaussy, “Up-scaling of Micro fibrillated Cellulose Based Positive Electrodes for Lithium Ion Batteries by Roll-To-Roll Printing Process,” order, vol. 5, no. 5, 2015.
[5] O. El Baradai et al., “Microfibrillated Cellulose Based Ink for Eco-Sustainable Screen Printed Flexible Electrodes in Lithium Ion Batteries,” J. Mater. Sci. Technol., vol. 32, no. 6, pp. 566–572, Jun. 2016.
*Corresponding author: Jürg Schleuninger