By Kyle Proffitt
September 25, 2024 | The second annual Nickel Institute Battery Day Virtual Event was held September 18, 2024, and saw coverage of a range of battery issues with a focus on nickel as it transits from mining to use in advanced high-energy batteries, and finally to end-of-life recycling to new life. Players from the mining and automotive industries, government, and academic institutions all participated to give their perspectives.
More Nickel, More Problems; How to Get the Most from High-Nickel Cathodes
Yang-Kook Sun, Hanyang University, delivered the first keynote presentation discussing high-energy Ni-rich cathode materials for electric vehicles (EVs). Sun reviewed how increasing the Ni content in NMC cathodes improves battery discharge capacity, up to the point that a LiNiO2 cathode has the highest capacity of the series, at around 250 mAh/g. However, as this capacity increases, cycle performance is harmed, and the higher-Ni NMC cathodes lose capacity faster after multiple cycles. The thermal stability also decreases. “It is impossible to develop the ideal cathode by just changing chemical compositions. However, we need cathode material with high capacity and good cycle life and safe materials,” Sun said. In line with this, he said we must understand the capacity fading mechanism of lithium nickel materials.
A source of this capacity fade, he explained, is contraction of the NMC material as lithium moves to the anode, which creates microcracks in the cathode at higher nickel content. This volume contraction is nearly 10% for LiNiO2. NMC811, he said, “contains a few microcracks, which are trapped in the particle core.” However, NMC95 and pure LNO increased the extent of these microcracks, which then propagate to the surface of particles. Additionally, parasitic reactions of Ni4+ with electrolyte produce an impurity phase on the cathode surface. When cracks form in the particle surfaces, electrolyte can further penetrate and amplify these reactions and associated cathode degradation.
Sun’s group, working over the last 23 years, has developed methods for improving the cathode and counteracting these degradative forces. In a first approach, a Ni concentration gradient was used; the nickel content can be very high in the center of cathode particles, but particles are prepared with a gradient toward a low Ni-content surface, limiting parasitic reactions and microcrack propagation. Sun says you may have already benefitted from this technology. “Our concentration-gradient material has been licensed to Korean companies and has already penetrated the EV markets,” Sun said, pointing to Kia and Ford models that use the gradient cathodes. He showed primary data where NMC90 prepared with a concentration gradient retained 88% capacity after 1000 cycles, whereas uniform NMC90 cathode showed only 68% retention and much greater particle cracking in electron microscopy images.
Sun’s group continued to refine this approach by doping in other transition metals such as Sb, Nb, and Mo. With Sb-doped particles and the same Ni gradient, they achieved 88% capacity retention after 1,500 cycles and even nearly 80% retention at 2,500 cycles—far beyond typical EV standards. These dopants work, he explained, by controlling the microstructure of particles, converting from randomly oriented polygons to more radially oriented rod-like structures. According to Sun, these rod-like structures are better at dissipating internal stress associated with volume changes, and the diffusion paths for lithium ions also become more direct.
Sun also presented work from a January Nature Energy publication (DOI: 10.1038/s41560-023-01403-8), in which they introduced washing processes for cathode particles, first with Co-dissolved water to remove residual lithium after charging and form a protective coating, and then with NH4F to fluorinate the surface. This procedure greatly reduced residual lithium in cathode materials, and most impressively, it enabled 83% capacity retention after 3,000 cycles and 65% retention at 6,000 cycles, again greatly surpassing typical EV use. These modifications were also associated with major reductions in gas evolution and cell swelling.
U.S. Government Incentives to Strengthen Local Battery Supply Chain
The second keynote for the day was delivered by Ashley Zumwalt-Forbes, U.S. Deputy Director for Batteries and Critical Materials with the Department of Energy. She discussed her role in the Office of Manufacturing and Energy Supply Chains (MESC) and gave an overview of U.S. government involvement in the supply chain strategy around batteries. MESC was formed two years ago as a result of the Bipartisan Infrastructure Law and the Inflation Reduction Act. “We truly are the tip of the spear from a US government perspective on investing and building up the battery supply chain,” she said. Across MESC, $20bn of capital is available in tax credits and grants.
The batteries grant program that she oversees focuses on battery material processing and recycling grants. One of MESC’s goals is to eliminate vulnerabilities in the U.S. clean energy supply chain. Much of this comes down to incentivizing projects in the U.S. to reduce reliance on other countries, especially foreign entities of concern (FEOCs), and especially for critical energy materials (including nickel) and their processing. “We’re working to build up capacity all across the supply chain across the U.S.,” Zumwalt-Forbes said.
However, she explained that investments need to be made wisely. “We are capitalists,” she said, “our businesses have to make money to continue operating. My greatest fear is that capital would flow into projects and we build capacity, only for that capacity to shatter on day two because of negative economics.” She continued, “We need to understand what the cost basis is in the U.S. vs. internationally, what various benchmark prices are, and how we can potentially bridge that gap, make sure we’re choosing projects that are economic now and in the future.” She explained part of that difficulty, saying “the last 24 months have been brutal really across the commodity space.”
The MESC grants are set up to match private investment. “Our grants have to be at least 50% cost share from private industry; as private industry spends a dollar, government matches with up to a dollar,” Zumwalt-Forbes said. MESC is also set up for funding primarily commercial-scale operations. “We need to have seen a pilot plant, we need to have seen results in order to fund a grant application or a tax credit application,” she said. Another area Zumwalt-Forbes highlighted is how MESC is supporting education in these areas to bolster the ecosystem. “There is a substantial effort within MESC to build up industrial training centers, partnering with universities, but also with community colleges and trade schools,” she said.
She gave an overview of the US ecosystem as a whole for battery manufacturing, showing that more than $120bn of investment has been announced in the U.S.—though MESC is not involved in all of this. Based on her slides, MESC has specifically catalyzed $3.9b in private sector development, created >9,000 construction and permanent jobs, and enabled more than 1.3 million EVs annually.
She highlighted some of the funding she’s been involved with. “In Round 1 of the batteries grants, we funded two concentrators—that is what we would designate as the earliest part we can fund—all the way through cell-to-pack manufacturing, and it picks up on the back end with recycling.” These funded projects can all be reviewed at their website. She said with about $1.9bn in investments, “we made investments across that supply chain.”
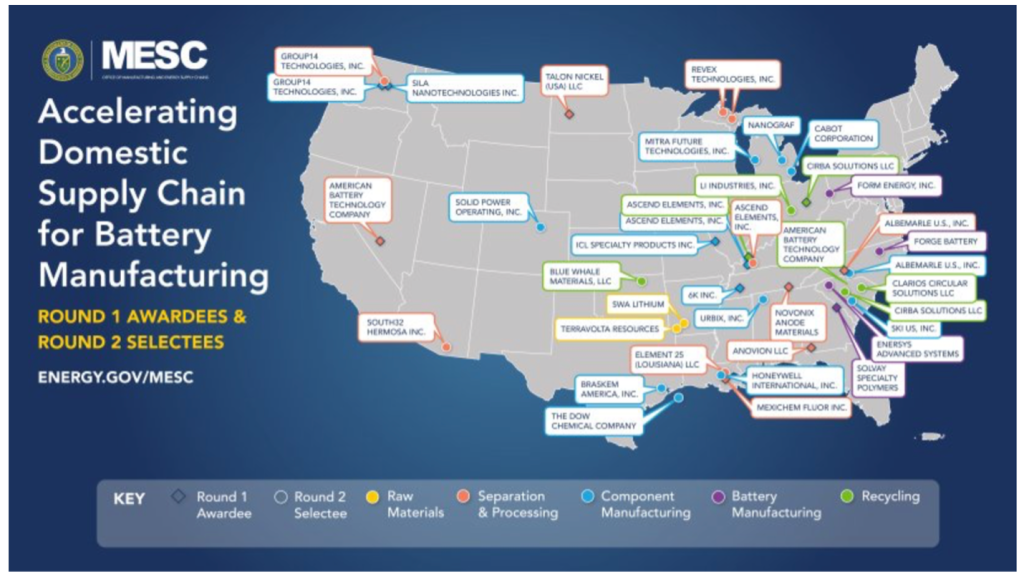
Funding opportunities are still available, such as 48C round 2, with $6bn. After her presentation, round 2 selections for the battery grants were announced totaling more than $3bn. For companies to better tailor their applications and know what MESC is looking for, she advised visiting their website and subscribing to the newsletter.
General Motors on a North American Battery Material Supply Chain
Michael Maten, Director of EV Policy & Regulatory Affairs at General Motors, gave an update on inroads for EVs, echoing many of the concerns Zumwalt-Forbes expressed in terms of supply chain issues and trying to increase local sourcing. Maten began by pointing to several newer or coming-soon EV models in the GM lineup, including trucks, delivery vans, and SUVs. “Our all-electric product onslaught is on,” he said. “To feed that ever-expanding portfolio, GM has done a great job over the last several years investing in battery cell manufacturing and our supply chain.”
Much of that, he says, has involved a move toward creating an ecosystem for battery materials here in North America, predating the Bipartisan Infrastructure Law and the Inflation Reduction Act, but spurred onward by these measures. He pointed to several examples. “Our cell plant in Warren, Ohio, is operating today, feeding all of our EV manufacturing plants. Our EV cell manufacturing facility in Spring Hill [Tenn.] is also open and operating. Our EV cell manufacturing facility in Lansing will be open next year. And you might have seen that we just finalized a deal with Samsung SDI, a second joint venture, $3.5bn, in New Carlisle, Ind.”
Headlines from 2024 also show this push toward more local supply chains, including an agreement with Redwood Materials for recycling battery scrap, a $150 million deal with Nouveau Monde in Canada for preparing all-natural graphite for anodes, and a deal with LG chem for a cathode active material plant in Clarksville, Tenn. However, global partnerships remain necessary, and Maten discussed several international agreements for sourcing lithium, nickel, cobalt, and manganese.
Maten said that GM has secured captive processing partnerships in North America, because “midstream processing is really important, making sure that we can get the cathode active material, the anode material, to meet our demands out to 2030 and beyond.” He reflected at the end of his talk on some of the supply chain challenges. Significant growth in production capacity across the battery value chain has occurred in Asia, and “overcapacity, quite frankly,” leading to significantly lower commodity prices. While that’s a good thing, he said, because prices are lower, “it creates an uncertainty in the market in terms of what those projects are going to be able to realize from a market pricing standpoint and makes it difficult for those projects to raise further funding.”
“How do we de-risk these projects?” he asked. “There’s national security benefits, sustainability benefits to bringing these projects closer to North America—how do we do that cost-effectively, given some of the overcapacity in Asia?” He says they are working on answering those questions, but closed by reaffirming that GM is, “fully committed to building a secure, sustainable, and scalable EV battery supply chain in North America.”
Making it All Circular
Bart Verrecht, Senior Program Manager, Umicore gave an update on battery recycling from an industrial perspective, providing useful information about the economic drivers and technical challenges involved. Although Umicore began as a mining company, they eventually added recycling capacity. “Historically we focused mainly on recycling of precious metals,” Verrecht said. However, he says “battery recycling will be the next big growth driver in that business area.”
The value of battery recycling comes in part because it can close the loop and create a true circular ecosystem. Additionally, “you can produce secondary metals with a lower carbon footprint than from primary sources,” Verrecht said. Finally, recycling helps tackle resource scarcity, recovering lithium, cobalt, and copper.
Verrecht showed a graph of end-of-life EV batteries and production scrap available for recycling, projecting a 27.1% compound annual growth rate. Umicore expects the share of recycling from end-of-life batteries to increase to about 40% by 2030 and to become the dominant source thereafter. He also showed projections for Ni demand and supply from primary and recycled sources, with an expectation that recycled supply will begin to outpace primary supply around 2047. EU regulations aim for 70% battery recycling efficiency by 2030 and requirements for OEMs to use 20% recycled Co, 12% recycled Ni, and 10% recycled Li by 2035. Verrecht sees these requirements pushing recycling efforts onward.
There are, of course, challenges. “We are currently really in a challenging environment for battery recycling… EV adoption, especially in Europe, is slower than expected.” Verrecht showed headlines where Umicore, Northvolt, and BASF have taken steps back in the last few months, placing different recycling projects on hold. Another area he wanted to draw attention to is the different battery chemistries involved. “The EU value chain is very much focused on NMC chemistry, while we now see that LFP is gaining more and more traction, not only in China but also in Europe.” Unfortunately, recycling LFP is more complicated, because lithium is the only real value component, whereas for NMC, there is a lot of residual value for the metals, which can exceed recycling costs and make recycling profitable. For LFP, Verrecht said, a gate fee may be required to ensure materials will be recycled.”
Verrecht said Umicore has been working on battery recycling in R&D since the mid-2000s, creating a large industrial pilot in Hoboken, Belgium, that has been operating since 2011. Significant upgrades were needed since 2022 to shift from small consumer electronics to EV batteries. For their process, Umicore typically dismantles batteries to the module level. Next, a pyrometallurgy step removes many of the impurities, producing a pure alloy of metals and simplifying downstream hydrometallurgical processes. This approach is distinct from others who shred batteries and prepare black mass first. Verrecht reported end-to-end recycling rates of >95% for Ni, Co, and Cu, and >80% for Li, returning these materials to battery-grade. He also said that despite what you might expect from an initial furnace step that generates significant CO2, their published analysis shows that their method produces less CO2 compared with other mechanical-pyrolysis-hydro methods that create black mass first.
Verrecht wanted to remind the audience that batteries are a lot more than metallic ores. In a hypothetical example, he showed a 500-750 kg battery pack, made of 10-20 kg modules, containing pouch cells accounting for about 75% of this weight. The remainder is casing materials. Then, only about 32% of the weight for the pouch cells is NMC; metal foils, electrolyte, graphite, and other materials make up the remaining bulk. Completing this calculation, a 500-kg battery pack contains only 120 kg of NMC. Beyond this, he said that there is a lot of diversity in packing and materials, and the value proposition changes accordingly.