By Kent Griffith
May 9, 2024 | Few subjects are more discussed regarding the electric energy transition than raw materials for lithium-ion batteries. The standard short-list includes lithium, cobalt, nickel, manganese, copper, aluminum, and graphite. New mines, processing techniques, and recycling initiatives are underway to sustain the availability of these critical resources. Another approach, highlighted by many at the recent International Battery Seminar and Exhibition, is the development of alternative electrode materials, electrolytes, separators, and current collector metals. At the event, representatives from Nippon Steel Chemical and Materials Co., Feon Energy, Celgard, BenQ Materials Corporation, Dimien, and Enovix shared their innovations in these areas.
Nippon ChemMat’s Current Collectors
Current collectors are often overlooked cell components that serve an important function: delivering electrons to and from the active electrode materials. They are also the largest source of inactive material mass inside a battery cell. Aluminum, used as the cathode current collector in lithium ion batteries, comprises about 5% of the cell mass while copper, used as the anode current collector, is heavier and thus adds up to about 10% of the cell mass (Figure 1). Rather unexpectedly, the presentation by Nippon Steel Chemical and Materials Co. at the event brought an entirely fresh perspective on the possibilities of metal current collectors. Nippon ChemMat has been developing stainless steel foils, with or without nickel plating, down to 10 µm thickness. Owing to its passivating coating, stainless steel can be used as the anode and/or the cathode current collector and shows similar or better capacity retention than aluminum with standard cathode materials such as NCA. On the anode side, stainless steel is about 10% lighter than copper for the same thickness of current collector. More importantly, the mechanical properties of stainless steel mean that it can withstand the strain coming from the large volume changes associated with silicon or silicon oxide anodes. Nippon ChemMat showed silicon cycling data for 10 µm stainless steel with 99.7% capacity retention after 50 cycles to 2760 mAh/g—far more stable than 18 µm copper under the same conditions.
Another underappreciated reality is the environment present in some solid-state battery cells. For example, sulfide solid electrolytes react with copper current collectors to form insulating copper sulfide. Stainless steel, on the other hand, is stable in the presence of hydrogen sulfide gas at ambient temperature. The downside: Nippon ChemMat estimates the price of 10 µm stainless steel foil is about 10 times that of copper because of the difficulty rolling the steel thin.
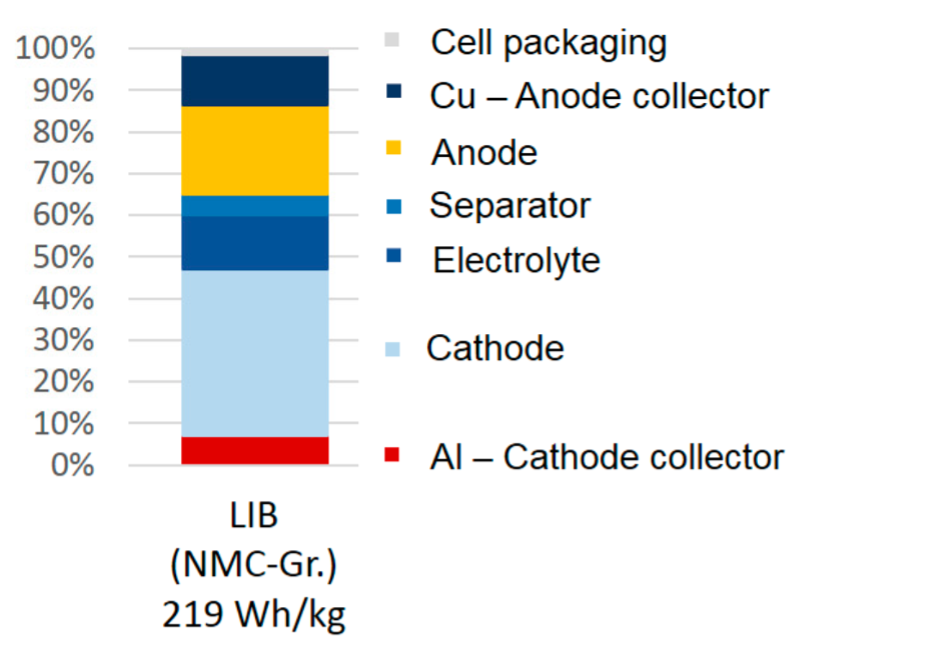
Innovation in Electrolytes and Separators
Another “inactive” pair of components of the cell are the electrolyte and the porous separator that hosts the liquid electrolyte in conventional lithium-ion batteries. Zhiao Yu of Feon Energy described the company’s journey toward new liquid electrolytes. Feon spun out of Stanford University in 2022 and set up shop in Woburn, Massachusetts. Feon is a small team of just eight people, but is already developing parallel product pipelines, one for lithium metal anodes and one for high-voltage cathodes. Specifically, Feon is bringing new electrolyte molecules to the field that convey properties such as high and low voltage stability, nonflammability, and dendrite suppression.
Moving on to the sponge that absorbs the electrolyte and facilitates ion transport between cathode and anode, John Zhang, CTO of Celgard, gave insights from the highly secretive separator industry. Celgard is well-known to battery scientists and engineers as the industry standard separator material, though most probably know very little about this thin polymer layer. Celgard produces various separators, mostly monolayer or multilayer sheets of polypropylene (PP) and/or polyethylene (PE). Zhang explained that Celgard uses a dry process to produce separators with a lamellar structure (Figure 2) that resist compression and thus maintain a steady pore volume for electrolyte storage, and a steady electrolyte conductivity, during active material expansion. Another Celgard technology that is widely deployed in commercial batteries is the trilayer PP/PE/PP with a central porous PE layer that expands when the cell temperature rises to unsafe levels, thus blocking the passage of any further current through the cell. This passive safety mechanism is just one of the modifications in use today. Zhang himself holds early patents on ceramic-coated separators, which is a technology that he says is used in virtually all consumer electronics and electric vehicle batteries today.
So what is coming next for Celgard? Separators that can block lithium metal dendrites to enable higher energy density lithium metal batteries. Also, enhanced wettability separators and permanently wettable separators that are easier to use and work with a wider range of electrolyte solvents. Separator technology was also discussed by Wei-ting Yeh, BenQ Materials Corporation. Yeh showcased alternative polymer/ceramic separators such as alumina particles coated onto polyimide (PI). Yeh highlighted advantages such as high performance in a thin (12 µm) separator, temperature stability up to 330 °C, and delay on thermal runaway. Like Zhang, Yeh also highlighted the importance of compression resistance for a good separator.
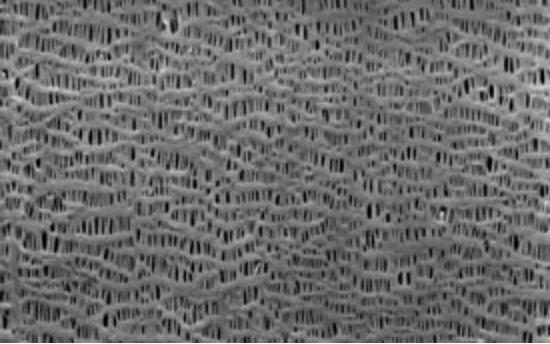
Novel Cathodes & Anodes
On the cathode side, Brian Schultz, CTO of Dimien, unveiled the company’s truly novel cathode material. Compositionally distinct from all the usual cathodes based on nickel, manganese, cobalt, and iron (NMC, NCA, LFP, LNMO, LCO, etc.), Dimien is developing a cathode based on vanadium. ZVO–zeta vanadium oxide–was invented at Texas A&M University and is used as a conventional intercalation cathode meaning that it hosts and releases lithium ions with minimal changes to its crystal structure. Thus, ZVO is not related to redox flow batteries, which is typically where vanadium comes up in battery conversations. According to Schultz, ZVO could exceed the energy density of LFP and even rise to a comparable level to NMC811. ZVO, like LFP, has a lower voltage than NMC, but the vanadium cathode compensates for its lower electromotive force by storing more lithium ions, up to 400 mAh/g. Schultz acknowledged that the 400 mAh/g may not be practical because it is only reached when the cathode goes down to 1.8 V, but he believes the capacity of 280 mAh/g from 3.8 to 2.2 V will be competitive.
Additional advantages of ZVO are that it does not undergo the typical oxygen release and thermal runaway of NMC cathodes and there is an established domestic supply chain for vanadium in the United States. A unique disadvantage to the technology is that it does not contain lithium, as synthesized, so it will have to be pre-lithiated or paired with a lithium metal anode. An early application for the Buffalo, NY-based startup based is wearables for the military.
Among the emerging silicon anode technologies, Enovix is developing a “100% active Si” anode that uses silicon oxide in a 3D architecture with integrated constraints to manage the extreme volume expansion and contraction that silicon experiences upon lithiation and delithiation. Late last year, Enovix aquired Routejade, a Korean battery manufacturer with more than 20 years of experience supplying medical, consumer, and industrial batteries. In his presentation, James Wilcox, VP at Enovix, explained that this move is aligned with the company’s strategy to bring their tech to non-EV markets at a rapid pace; for example, consumer electronics, drones, and robotics. This is an alternative to the longer term high-risk, high-reward strategy of many battery and component developers who are targeting the appealing but elusive passenger EV market.
Innovations are underway for every single component of lithium-ion batteries, let alone the plethora of technologies beyond lithium that are under development. As ever, the future for batteries is not convergence toward a mythical holy grail but divergence toward a smorgasbord of choices that can be tailored to every existing and emerging application.