By Kent Griffith
April 14, 2022 | It was Tuesday, October 10, 2017, when Jeff Dahn’s team at Dalhousie University started cycling a batch of batteries. When they checked on those cells on March 27, 2022, they had reached nearly 15,000 cycles with only 5% loss in capacity. Considering an EV with 250 mi range, these results would translate to a driving range of 3.75 million mi with plenty of life remaining.
Thus opened Jeff Dahn’s plenary lecture at the 2022 International Battery Seminar. The conference was held at the end of March 2022, just over two years after the world shut down in response to the Covid-19 pandemic. The energy was palpable as the battery community came together in record numbers for the 39th International Battery Seminar. While the industry has been busy expanding despite the pandemic, there was a renewed sense of community for those who were able to come back together in person.
Dahn is the NSERC/Tesla Canada Chair at Dalhousie and has been in a research partnership with Tesla since 2016. He is also the CSO at Novonix, a spin-out with high-precision battery cyclers and artificial graphite products.
How did Dahn’s laboratory get to batteries that can cycle for millions of miles? According to Dahn, with a combination of single-crystal NMC532, good artificial graphite, appropriate electrolyte additives, keeping the upper voltage cutoff low, and being lucky. NMC532 is a cathode material with metal content of 50% nickel, 30% manganese, and 20% cobalt (LiNi0.5Mn0.3Co0.2O2). Because state-of-the-art batteries with high energy density contain 80% nickel or more, NMC532 may not give maximum range, but the extremely long lifetimes would be well suited for vehicle-to-grid (V2G) applications, which Dahn says is a future must. V2G would provide energy storage for the grid, allowing vehicles to store intermittent renewable energy from solar and wind and moving us toward a cleaner and more sustainable future.
Diving into the details behind Dahn’s criteria for a long lifetime battery, it is important to understand the inherent relationship between energy and both nickel content and upper cutoff voltage (UCV). For a fixed UCV, the accessible lithium and thus capacity will increase as nickel content increases. For instance, an NMC532 cell charged to 4.40 V may give the same capacity as an NMC811 (80% Ni, LiNi0.8Mn0.1Co0.1O2) charged to 4.15 V. Using these relationships, Dahn showed that NMC811, a cathode material known for stability issues when cycled to high energy at 4.2 V, is extremely stable when cycled to a lower voltage of 4.06 V. Stopping at 4.06 V prevents the cathode material from undergoing the so-called H2-to-H3 phase transition associated with a large strain that leads to particle cracking (Figure 1).
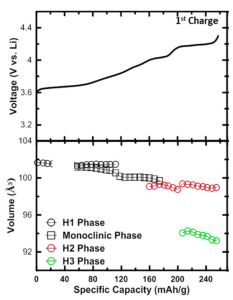
In his plenary, Dahn went further and presented a road map to batteries with a lifetime of 100 years. Surprising to many, this century battery is an NMC chemistry. As Dahn puts it, “Conventional wisdom: Everyone knows LFP//graphite cells have longer lifetime than NMC//graphite cells. Question: Why are you telling us about NMC//graphite cells? Are you wasting our time? Answer: Conventional wisdom is not always correct[.]”
Dahn showed that the best known commercial LFP//graphite cells and their most optimized LFP//graphite cells with favorable LiFSI electrolytes and additives cannot match the capacity retention of NMC811 charged to 4.06 V or NMC532 charged to 4.3 V. While the lifetime with LiFSI salt is excellent—better than the conventional LiPF6 salt—LiFSI corrodes the aluminum current collector at full cell voltages above ~4.0 V. What Dahn’s team then did was prepare cells of NMC532//graphite, NMC811//graphite, and NCA92 (92% Ni)//graphite that were balanced to reach a negative electrode capacity to positive electrode capacity ratio (N:P) of 1.05 at a desired UCV from 3.7 to 4.1 V. In other words, less graphite is used than in a conventional cell, allowing the graphite to be filled at a lower voltage without removing as much lithium from the cathode. By building NMC and NCA cells designed for lower voltage operation with LiFSI salt, they were able to reach energy densities above that of LFP//graphite while staying below 4.0 V, and they project lifetimes of more than a century (Figure 2). A century of C/3 cycling equates to approximately 146,000 cycles.
We’ll check back with Jeff on October 10, 2117.
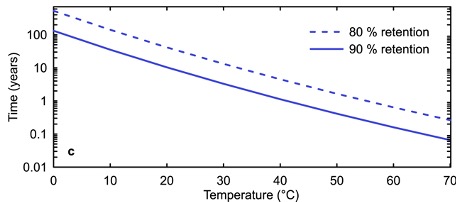
Electrification at LG
In her plenary, Denise Gray, LG Energy Solutions, shared LG’s vision of electrification. Gray is a veteran of the automotive and battery industries. She moved to LG in 2015 after short stints at AVL and Atieva following nearly 30 years at GM. With the spin-off of LG Energy Solutions from LG Chem in December 2020, Gray took on the role of President of LG Energy Solutions Michigan Tech Center. The US tech center complements Korean, Chinese, and European tech centers in Daejeon, Nanjing, and Frankfurt, respectively. As LG ramps up production, they have already committed to 200 GWh annual production capacity in North America. She described future EV requirements of 600 km (375 mi) range, purchase parity with conventional internal combustion vehicles, 80% charging in less than 20 minutes, a lifetime of at least 10 years and 300,000 km (185,000 mi), and no safety issues. It is interesting that she emphasized purchase parity between EVs and combustion vehicles, not cost of ownership, since EVs benefit from greatly reduced energy input costs and lower maintenance costs. It is certainly the case that consumers may not do this accounting upfront, and sticker price will continue to influence consumer decisions for some time.
Debate looms large as to the optimal cell design among pouch, cylindrical, and prismatic form factors. Cylindrical forms remain in the minority with the notable exception of Tesla and the vocal Elon Musk announcing that Tesla is strongly against the pouch format. To meet customer demands, LGES is producing both cylindrical and pouch cell formats.
Cell performance and cost are critical, and developments are underway on both fronts. LGES is pushing coated nickel-rich NCMA (nickel, cobalt, manganese, aluminum) cathodes to enhance energy and safety. They are also developing silicon-containing anodes and boast the world’s first mid-sized cell application of surface-treated metal–silicon–oxide anodes. At the cell level, LGES has cells with large surface area, integrated cooling, and a low profile design, all which should help with thermal management. Long cells, while harder to manufacture, are also available to simplify EV pack design. Under pressure from lower cost segments of the market, LGES is pursuing lower cost cathode chemistries such as lithium manganese oxide (LMO, LiMn2O4) and lithium iron phosphate (LFP, LiFePO4), a solvent-free process to make high-loading electrode coatings, and module–pack integration that saves on structural components.
I’ll leave the closing thought to Gray who conveyed the state of the field concisely when she said, “What an exciting time for all of us… who are a part of the battery industry. It has been a long journey and there is still so much to be done.