By Kent Griffith
September 7, 2021 | The virtual Solid-State Battery Summit brought together leading OEMs, established and start-up battery materials and cell manufacturers, analysts, and institutional researchers earlier this month to discuss progress and challenges on the road to solid-state lithium-ion batteries. The field carries huge momentum, looking to replace the flammable liquid electrolyte and polymeric separator in state-of-the-art lithium-ion cells with a solid-state separator, typically a non-flammable oxide or sulfide ceramic or glass. Beyond the safety advantages, solid-state battery stakeholders hope to enable the use of higher energy density materials such as higher capacity anodes and/or higher voltage cathodes, thereby increasing driving range in EV applications—the primary target market for solid-state cell makers.
General Motors was represented at the Solid-State Battery Summit by Dr. Fan Xu, who portrayed a role for solid-state batteries beyond enabling new electrode materials. GM is interested in the prospect for higher packaging efficiency and design flexibility afforded by solid-state batteries and the opportunity to leverage bipolar design (Figure 1). This, combined with the simplified thermal management that may be possible with solid-state batteries, could increase battery-to-vehicle integration efficiency. Xu did note that it is too early to predict how solid-state technology would affect the EV battery warranty. She described a series of commonly discussed challenges with solid-state battery development and adoption including interfacial resistance, cycle stability, volume change, large-scale manufacturing, and cost competitiveness, as well as some less commonly discussed issues to consider such as the diagnosis and prognosis of the battery state of health with new battery materials.
Adrian Tylim from Blue Solutions was able to offer a rather unique perspective as Blue Solutions is the only company with a solid electrolyte and lithium metal anode operating in the commercialized EV space today. The Blue Solutions lithium metal polymer battery pairs a lithium iron phosphate (LFP) cathode with a lithium anode, the two separated by a dual electrolyte with a polyethylene oxide (PEO)-based solid polymer and a catholyte. As is well-known in the field, PEO is not sufficiently conductive to lithium ions at room temperature, so the Blue Solutions cells run at an internal temperature of 80 °C. The LFP cathode is more stable against the polymer than higher energy materials such as layered oxides based on nickel and cobalt; however, the lower energy of LFP means that this technology does not achieve the high energy densities sought by other solid-state battery firms. Nevertheless, Blue Solutions, part of the Bolloré Group, is an example to the field with over a decade of experience manufacturing and deploying solid-state batteries for EVs, as well as experience assembling modules into large packs for stationary grid storage.
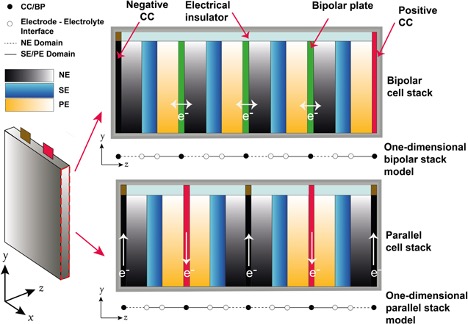
In addition to keynote presentations from QuantumScape and Solid Power, new solid-state battery platforms were presented by Steve Visco of PolyPlus Battery Company and Lisa Hsu of ProLogium. PolyPlus is developing a glassy sulfide solid electrolyte. With a nod toward scalability, they have moved from pressing sulfide glasses to a roll-to-roll processing method. An example cell described by Visco contains 2 µm lithium applied to the sulfide glass with a liquid electrolyte, called a catholyte, to facilitate wetting between the solid electrolyte and cathode material. One advantage PolyPlus sees in glasses is that you can achieve surface roughness below 1 nm, which both Visco and Paul Albertus, University of Maryland, noted is critical for joining solids and cycling lithium at high current densities.
On the subject of catholytes, Richard Clark from Morgan Advanced Materials remarked that he views liquid on the cathode side as a pragmatic but non-ideal solution to the interfacial contact problem, something that is likely a steppingstone but will still be eliminated in the long term. ProLogium described an oxide separator that they coat as a wet film. Like QuantumScape and PolyPlus, ProLogium does use a catholyte, in this case a 90/10 mixture of solid/gel. Like Solid Power, ProLogium is developing silicon-based anodes while also working toward the eventual target of pure lithium metal. Among the bolder ideas put forth, ProLogium envisions single, enormous, bipolar cells with 80–100 kWh, a technology they are calling “cell-in-pack”. This design would afford much higher pack assembly efficiencies and thus higher pack-level energy densities than traditional assembly or the cell-to-pack designs.
Along the theme of silicon anodes for solid-state batteries, Felix Hippauf of Fraunhofer IWS presented some fundamental insights on the use of silicon with sulfide solid electrolytes. According to Hippauf, the classic slurry deposition method involves timely and expensive drying steps and is particularly not ideal for sulfide electrolyte processing because the sulfides are not stable in the typically used solvents. Instead, researchers at Fraunhofer have developed a dry processing method that is suitable for sulfides and high electrode loadings.
Jordi Sastre, recent graduate of Empa, the Swiss Federal Laboratories for Materials Science and Technology, has spent years developing thin-film garnet solid electrolytes with high lithium-ion conductivity, cathode–electrolyte interface stabilization with niobium oxide and dendrite suppression with amorphous garnet. Another interesting development on the academic front came from Xin Li’s laboratory at Harvard University. Li described the mechanical constriction effect in solid-state batteries, which he believes offers the possibility to enhance the local voltage stability and stabilize solid–solid interfaces. Michel Armand, a major contributor to the development of lithium-ion battery technology since the beginning, shared his laboratory’s latest work on polymer-based electrolytes for solid-state batteries. Armand has been working to overcome the elevated temperatures required for solid polymer batteries by developing new polymer electrolytes based on Jeffamine compounds. New lithium salts are also being investigated that lead to longer cycle life and lower overpotential with conventional PEO-based solid polymers.
Keith Beers from Exponent provided insights on what may be to come for solid-state battery safety and qualification testing. Since the technology is still evolving, early testing is and will be largely similar to lithium-ion batteries, but modifications should be expected particularly around the physical properties of lithium metal, which melts at only 180.5 °C. Beers notes that while solid-state batteries do fail more safely under select tests and conditions, the presence of lithium metal and its increased reactivity upon melting mean that solid-state lithium metal batteries can exhibit worse safety failures than conventional lithium-ion batteries. Beyond all the mandatory and voluntary industry standards, Beers reiterates that the goal is to avoid failures in either safety or performance.
Michael Sanders, a battery veteran of DuPont and currently an analyst at Avicenne Energy presented a cautious outlook for the solid-state battery commercial market. He noted that several major players including Apple, Seeo (under Bosch), Sakti3 (under Dyson), and Fisker have exited the solid-state battery business. At the summit, Sanders stated, “Partnership risk is still high as the technology is still in development and capital investment for production may be higher than lithium-ion batteries. It will also be difficult for solid-state [batteries] to compete with lithium-ion battery costs.” The decreasing costs of conventional lithium-ion batteries present a moving target for solid-state battery developers, a challenge echoed by Ines Miller of P3 Automotive. She noted that solid-state battery costs could be higher or lower depending on the material selections and manufacturing processes. From the performance side, too, Sanders was chary of the benefits, “Solid-state technology has the promise of providing better safety for larger formats, but we are not convinced that solid state will provide longer life, a smaller battery, lighter battery, cheaper battery.” Avicenne sees a long path toward the automotive launch of solid-state batteries, with the need to establish large cell pilots and commercial production, close battery durability and performance gaps, consider the effects of pressure on pack design, build, and test a significant number of prototype vehicles, and perform extensive vehicular safety testing to understand and mitigate risk.