By Kent Griffith
February 20, 2020 | In an effort to increase the driving range of electric vehicles and other battery-powered devices, the search is on for new materials that can store more energy than the graphite anode in modern lithium-ion batteries. Rechargeable batteries with lithium metal anodes could represent the ultimate limit in energy density. However, lithium metal anode adoption faces considerable technical and safety hurdles. Their high energy density means they are liable to react with other components in a battery cell and to mechanically break down through large volume changes. Furthermore, lithium metal anodes are particularly susceptible to the phenomenon of dendrite formation where a lithium metal wire can grow off the surface of the anode and short-circuit the battery, causing rapid heat generation and potentially a fire or explosion.
Lithium metal anodes are not a new concept. In fact, they were used by 2019 Nobel Laureate Stan Whittingham in the first lithium battery cells in the late 1970s. However, the aforementioned setbacks created the need for a safer and more stable anode, which set the stage for the development of carbon materials by co-laureate Akira Yoshino. Graphite has been the anode of choice since the successful commercialization of lithium-ion batteries by Sony in 1991. So, why are we back to lithium metal? The answer lies in the fact that pure lithium is still the best, in theory, if its problems could be overcome. Another important factor is the demand for the electrification of cars, buses, and aircraft, which is exceptionally challenging and is pushing battery engineering and materials to their limits.
Various claims surround the impact of lithium metal anodes. The lithium that is cycled in a lithium-ion battery comes from the cathode. The existing graphite is simply a storage container for these lithium ions. In its ultimate form, we could get rid of the anode completely, and the lithium in the cathode could simply deposit as lithium metal on a thin sheet of foil. Others will claim an improvement in anode capacity of 10x based on the weight of lithium versus graphite. This does not translate to an 10x (or higher) increase in driving range! The anode only makes up about 20% of the weight of a battery cell, so even an “anodeless” battery would be limited to this relatively modest increase in energy unless changes are made to other cell components. In practice, there will likely be some sort of architecture and/or excess lithium that supports the lithium metal anode. Accounting for the size and weight of the architecture will further constrain the extent of the performance improvement. Nevertheless, even small advances to the forefront of lithium batteries are still extremely valuable in this rapidly growing multibillion dollar market.
With that perspective, it is possible to appropriately evaluate the report earlier this month on stable lithium metal batteries entitled, “Li metal deposition and stripping in a solid-state battery via Coble creep” published in Nature (DOI: https://doi.org/10.1038/s41586-020-1972-y). Professor Ju Li, MIT, and collaborators reported that materials that possess both ionic and electronic conductivity could serve as stable architectures for lithium metal. As a demonstration, carbon nanotubes were reversibly filled with lithium metal (Figure 1). In order to become good mixed conductors, the carbon tubes were coated with zinc oxide and then reacted with lithium. The authors report that such a coating is necessary to achieve uniform nanotube properties. At first pass, this may sound similar to lithium insertion into graphite in conventional batteries. While both cases describe lithium being stored in carbon, graphite stores relatively isolated lithium ions in individual layers while the nanotubes are storing regions of pure lithium metal with more than 100 million atoms. The authors show (Figure 2) that these carbon tubes should exceed the charge storage performance of graphite as long as the open volume of the tubular array is greater than 30%. Furthermore, the tubes can also store sodium with potential applications in sodium metal batteries, whereas graphite itself is not a suitable anode for sodium ions. The team published their research in Nature after a lengthy 21–month peer evaluation process.
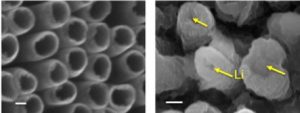
A central aspect of this study was the real-time analysis of the lithium filling process with an electron microscope. Through this advanced characterization, the authors determined that lithium travels through the tubes via a mechanical process known as Coble creep. This process is rather like lithium climbing up the interface of the tubes. More than an interesting finding, this means that lithium does not have to diffuse through the walls themselves, which greatly increases the number of options available for tubing materials. Suitable materials for the lithium storage tubes should have good mechanical strength and ductility, (nearly) metallic electronic conductivity, and chemical stability against lithium metal. Examples include alloys of lithium with graphitic carbon, silicon, and aluminum. Furthermore, as the lithium climbs, it was even observed to overcome defects partially obstructing the tubes.
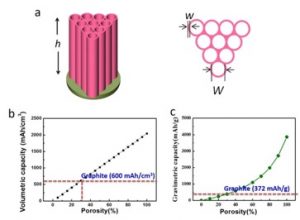
In a step toward practical applications, a full solid-state cell was constructed by depositing a tubular array of about 10 billion carbon cylinders through chemical vapor deposition onto a template. After etching away template, the carbon nanotube interiors were coated with zinc oxide via atomic layer deposition and then the whole array was capped with a solid-electrolyte layer. In a pre-cycling step, lithium was deposited into the tubes from a lithium metal counter electrode. Then, the full cell was completed by pairing the lithiated carbon electrode against a cathode comprising lithium iron phosphate (LFP). This solid-state battery was able to cycle metallic lithium with relatively high charge and energy efficiency compared to other lithium metal batteries.
An all-solid-state battery with a lithium metal anode was thus demonstrated to cycle reversibly and efficiently with an anode capacity nearly 3x that of graphite. Further testing would be required to see how this translates into commercial format batteries but perhaps a 10% improvement in cell energy density could be achieved. There are of course other challenges, particularly in terms of scalability and cost. While efficient and stable cycling is a necessity, the questions surrounding safety at high charging rates or non-ambient temperatures have not yet been addressed. Nevertheless, this demonstration, and the mechanism of lithium movement through mixed conductors, will spur further research and is a step in the right direction toward enabling lithium metal and all-solid-state batteries.