Contributed commentary by Alex Rawitz, Servato
Lead-acid batteries are the workhorse battery of standby power. Safe, reliable, and cheap, they dominate industries like telecom and utilities where backup batteries are essential in maintaining uninterrupted operations. Today, tens of millions of Valve-Regulated Lead-Acid (VRLA) batteries are in use at millions of sites across the country.Managing these batteries is not easy for the companies that buy them. Most of the time, the sites where these DC power systems are deployed are unmanned and remote. These deployment sites include remote broadband locations, railroad switching stations, or some other type of site where there is a durable cabinet housing industry equipment and the DC power system. In these cases, batteries are subjected to the elements: oppressive heat during the summer, cold during the winter, dust and humidity, animals, and more. The robustness of VRLAs to withstand these factors make them such a great choice in these applications, but the environmental pressures will affect reliability and battery life.
At certain sites the risk and uncertainty introduced by environmental factors is intolerable. In telecom, larger community nodes or Central Offices, which handle huge amounts of customer services and potentially critical public safety traffic, are a great example. If a power outage occurs and the batteries fail or even just underperform, the results could be costly or even tragic. In these settings, the environment must be controlled to ensure that all the equipment operates optimally and reliably.
What many people do not realize is that at these types of sites batteries are the primary driver of the temperature requirements. Network equipment is built to withstand very high temperatures. The batteries require special treatment because of the unique nature of their operational characteristics compared to other equipment. The life and operation of a battery is far more sensitive to temperature than any other piece of equipment, so to ensure that critical sites do not need constant battery maintenance and replacements, the set point is tailored to a range where battery work is minimized. Of course, achieving lower temperatures through HVAC is costly, and if battery reliability and operational life could be improved independently of temperature, cost savings could be passed through on cooling costs.
Why Are Batteries so Temperature Sensitive?
High battery temperatures reduce battery life, and as the temperature is increased the mechanisms that cause premature failure are accelerated. One such condition that contributes to short battery life is Float (continuous) charging. Positive grid corrosion is increased at the high electrode potentials required to keep the plate charged. Exothermic heat is produced by the oxygen recombination process, and dry-out results from electrolysis of water during continuous charge. Further, as heat increases, so does the rate of the following failure mechanisms:
- Positive grid corrosion
- Dry-out
- Active materiel degradation
The relationship between a batterys operating temperature and its expected life is described in Arrhenius equation and the Arrhenius curve.

Figure 1 illustrates clearly that the mechanisms that cause premature battery failure accelerate exponentially as the temperature is increased. The numbers are actually quite simple. At a constant float voltage, the life of the battery is reduced by half for every 10C (18F) increase in temperature.
This curve is the reason that critical sites are cooled so aggressively. A 10C increase in temperature from say 25C to 35C would not have a dramatic impact on the function or Mean-Time-Between-Failure (MBTF) of most network equipment, but it would halve the life of the batteries at the site. This is well known to battery manufacturers and buyers, and it is why they have made attempts to mitigate heat at sites beyond HVAC.
Solutions for Battery Heat Answers that Do Not Go Far Enough
Before we get to how changing charging methodology can allow for a much larger reduction in HVAC needs, we should cover some of the other ways in which operators have tried to minimize the effects of temperature on batteries and improve battery life. Despite the various approaches, most improvements have a minimal impact on battery life (and thus the ability to change temperature set point) because they are passive improvements. Table 1 summarizes some of these options, their positive effects, and shortcomings.
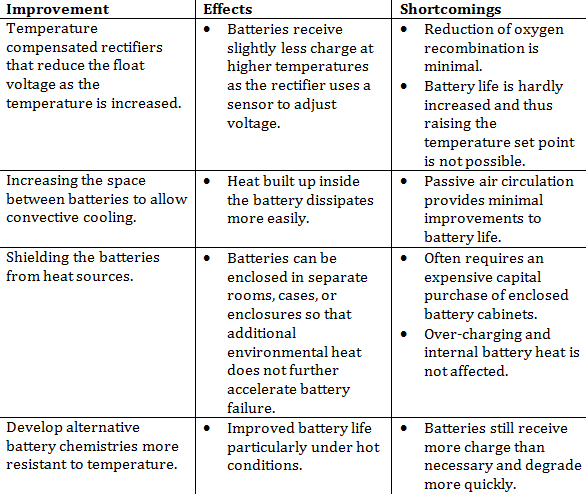
None of these have been completely successful since they add considerable cost and do not remove the sources of the heat: heat generated during the constant charging of the batteries.
The damaging consequences of overcharging have, in fact, been known for many years and it is normal practice in automotive and other battery applications to charge batteries only when necessary and then only for as long as necessary. Why, then, are standby batteries still subjected to continuous overcharge? There simply has not been a better alternative to float-charging until recently.
Adaptive Charging Extend Battery Life and Save Money on Cooling
The idea of Adaptive Charging is to charge batteries only when necessary and then remove them from charge to rest the batteries at all other times. While at rest, there is no oxygen recombination reaction and positive grid corrosion, dehydration and active material degradation virtually cease.
Adaptive Charging has been proven in several papers to extend battery life in VRLAs by approximately 100 percent and is shown below in Figure 2[1]. The solution monitors monoblocs and strings and manages charging by sitting between the rectifier and the bus to achieve the longest possible life. It determines battery state-of-health, identifies failing or failed batteries and removes strings with defective batteries from charging to prevent them from shortening the life of other strings. The solution only charges the batteries when necessary ensuring that the batteries are never over-charged.
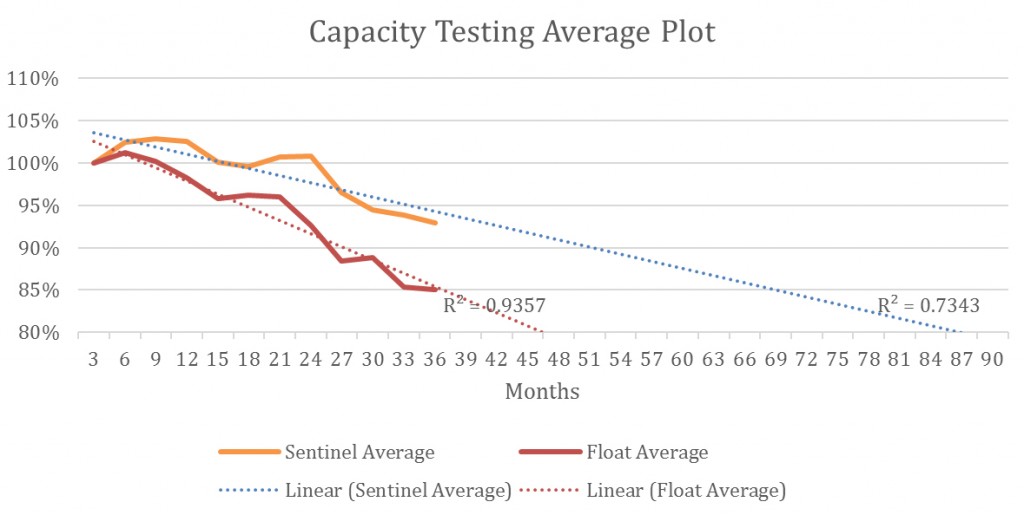
Crucially, Adaptive Charging has been shown to be temperature agnostic at normal site temperature ranges. This means that while in some deployments diversity of equipment and environmental factors will change the back-of-the napkin math, Adaptive Charging will have a predictable affect on the Arrhenius Curve. If Float-charged batteries lose half their battery life with a 10C increase in temperature, but battery life can be doubled again using Adaptive Charging, the result it’s a net 10C increase in temperature with no loss in battery life or reliability.
Any operations manager or technician will tell you that for most sites 10C or 18C is a very significant temperature difference as far as the dollar value of the cooling required to achieve it. However, they will probably also tell you that the value will vary dramatically site to site. Factors that affect it will be the cost of electricity, which ranges widely across the US, the efficiency of the HVAC system and environmental control, and the age of the batteries and the rectifier. Given all these factors, calculating expected savings can be tricky but based on conversations with industry experts the range of savings is somewhere between $100 and $1,000 per site per year.
The telecom industry has tens of thousands of sites that could benefit from these cooling cost reductions because of their HVAC requirements. For larger companies, the value of the savings over a 5 to 10 year battery replacement cycle could be huge. Early data is very suggestive, but still more data is needed to narrow the estimates on the impact of this technology.
As a side note, smaller sites without HVAC should not be summarily dismissed. Almost all of these sites use limited climate control, perhaps a heat exchanger or small fan, to cool the batteries. Using Adaptive Charging for battery life extension has been proven in the field to extend battery life and reduce maintenance costs here too.
Conclusion
Of all the equipment at telecommunications (and other industry) sites, batteries are the most sensitive to increases in temperature. Their chemistry is directly affected by increases in temperature, and the Arrhenius equation describes how battery life is halved with each 10C increase in temperature. It is the batteries that have warranted such heavy investment in HVAC at sites. With Adaptive Charging capable of doubling battery life irrespective of temperature, companies across industries have an opportunity to generate significant savings per site by increasing the temperature set point. The ball is in the hands of the technicians and managers who maintain the network and grapple with managing the costs every day.
Reference
[1] Battcon
Alex Rawitz joined Servato in 2015 and with years of sales, operations, and project management experience. Alex covers the Southeast sales territory for Servato while also spearheading business development, marketing, and other operational efforts. Prior to joining Servato, Alex managed entrepreneur programs at The Idea Village including the non-profits flagship accelerator programs, where he worked directly with over 100 entrepreneurs across a broad array of industries and alongside a dozen eminent New Orleans business leaders who were Entrepreneurs-in-Residence. Before joining The Idea Village, Alex was selected as one of 68 Venture for America fellows, an elite non-profit program that places college graduates at startups in emerging cities, helping build businesses, create jobs, and make an impact.
For more information, visit Servato.